不銹鋼管道因其優異的耐腐蝕性、高強度和長壽命,廣泛應用于石油化工、食品飲料、醫藥制造等領域。然而,表面質量問題(如劃痕、氧化皮、色差、焊縫缺陷等)仍是制約產品附加值與客戶滿意度的關鍵痛點。據統計,因表面缺陷導致的退貨率占不銹鋼管道質量問題的60%以上。本文將從原料選擇、生產工藝、設備升級及質量檢測四大維度,系統闡述如何從源頭構建表面質量防控體系,助力企業提升產品競爭力。
一、原料把控:選對材質是基礎
鋼種匹配應用場景
不同牌號的不銹鋼(如304、316L、2205雙相鋼)化學成分差異顯著,需根據介質特性(如氯離子含量、溫度、壓力)選擇合適材質。例如,沿海地區供水管道建議采用316L以抵抗氯離子腐蝕,避免表面點蝕引發的質量隱患。
原料表面預處理
原料卷材或板坯表面若存在油污、銹蝕或劃傷,會在后續加工中放大缺陷。企業應引入自動化清洗線,通過堿洗、酸洗、噴砂等工藝去除表面雜質,同時采用激光掃描檢測原料表面平整度,剔除不合格材料。
供應商分級管理
建立原料供應商白名單制度,定期抽檢其熔煉工藝、成分均勻性及表面缺陷率。例如,某頭部企業通過與鋼廠聯合開發“管道專用鋼”,將原料表面缺陷率從3%降至0.5%,從源頭減少了后續處理成本。
二、生產工藝優化:精細化控制是關鍵
成型環節:減少機械損傷
冷軋/冷拔工藝:采用多道次小變形量軋制,避免單次壓下量過大導致表面橘皮紋;冷拔后需立即進行脫脂處理,防止潤滑劑殘留引發氧化。
彎管工藝:使用中頻感應加熱彎管機,通過精準控制加熱溫度(850-950℃)和彎曲半徑,避免管壁減薄或表面褶皺。某企業通過優化彎管模具設計,將焊縫與彎曲軸線的夾角控制在45°以上,顯著降低了彎管區裂紋風險。
焊接環節:消除焊縫缺陷
自動化焊接技術:推廣等離子焊接、激光焊接等高精度工藝,替代傳統手工氬弧焊,減少焊縫余高(建議≤0.5mm)和咬邊深度(≤0.1mm)。
焊后處理:采用機械拋光+電解拋光組合工藝,先通過砂帶機去除焊縫飛濺,再利用電解液(如磷酸+硫酸混合液)進行表面整平,使焊縫區與母材光澤度差≤10%。
熱處理環節:控制氧化與脫碳
固溶處理時需快速升溫至1050-1150℃,并嚴格控制保溫時間(按管壁厚度1.5分鐘/mm計算),隨后水淬冷卻以防止碳化物析出。某企業通過在退火爐內充入氮氣保護,將管道表面氧化皮厚度從15μm降至5μm以下,減少了后續酸洗損耗。
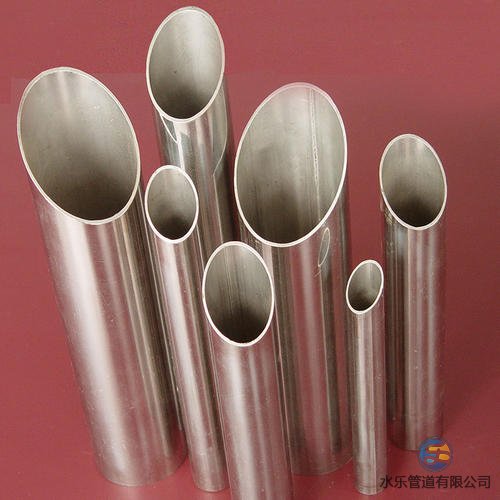
三、設備升級:智能化賦能質量提升
高精度加工設備
引入六軸數控機床進行管端倒角加工,通過編程控制切削深度(建議≤0.2mm)和表面粗糙度(Ra≤0.8μm),避免手工打磨導致的局部過熱變色。
在線檢測系統
表面缺陷檢測儀:采用CCD相機+AI圖像識別技術,實時監測管道表面的劃痕、孔洞等缺陷,檢測速度可達30米/分鐘,準確率超99%。
內窺鏡探傷:對彎頭、三通等異形件內部進行可視化檢查,及時發現裂紋或焊瘤,替代傳統射線檢測的耗時與輻射風險。
清潔生產環境
建設無塵車間(潔凈度等級ISO Class 7以上),配備空氣凈化系統和防靜電地板,減少加工過程中灰塵附著導致的表面瑕疵。某企業通過升級車間環境,將管道表面清潔度從Ra3.2μm提升至Ra1.6μm,滿足半導體行業嚴苛要求。
四、質量檢測與追溯:閉環管理防風險
全流程數據記錄
利用MES系統記錄每根管道的原料批次、工藝參數、檢測結果等信息,生成唯一二維碼標識,實現質量追溯至具體工位和操作人員。
破壞性抽檢與模擬測試
鹽霧試驗:按ASTM B117標準進行720小時中性鹽霧測試,驗證表面鈍化膜耐蝕性。
壓力循環測試:對管道施加1.5倍額定壓力的交變載荷,檢測焊縫區是否出現泄漏或表面起泡。
客戶反饋驅動持續改進
建立質量問題快速響應機制,對客戶投訴的表面缺陷進行根因分析(如通過SEM掃描電鏡定位裂紋源),并反向優化生產工藝參數。例如,某企業通過分析客戶退貨管道的焊縫金相組織,發現熱輸入過量導致晶粒粗化,隨后調整焊接電流,將焊縫沖擊韌性提升20%。
結語:源頭防控比事后修復更高效
不銹鋼管道表面質量問題的解決,需從原料選擇、工藝設計、設備投入到檢測追溯形成閉環管控。企業通過引入智能化技術(如AI檢測、數字孿生)和精益生產理念(如單件流、防錯設計),可顯著降低質量成本(通常占銷售額的5%-15%)。在高端制造領域,表面質量已成為客戶選擇供應商的核心指標之一,唯有從源頭筑牢質量防線,方能在激烈的市場競爭中脫穎而出。